Friday, January 6, 2012
Browse »
home»
Building Molds
My mold material was Spruce - but it seemed very green when delivered to my shop from the sawmill, with moisture content around 18%. So armed with my plans and my GLWB book, I set about assembling the molds. I decided to use biscuit joints to join the boards. John Brooks describes a method of using yard sticks joined together to work out the best angle to optimise the wood lengths. This was confusing initially, because I didn't appreciate the end product, so I stressed over this unnecessarily. I was introduced to the science and trigonometry of using a bevel gauge, transferring it to a Bevel Boss . I railed in my engineering minded friend Bendan to figure out how to transfer the measurements off my BevelBoss to my MitreSaw...
John shows how to create your own Bevel Boss in his book, but this tool has proven to be a very accurate companion for me and I am doubtful if I could have recreated this with the same level of accuracy.
The biscuit joints proved to be insufficient and unnecessary so I ended up adding the blocks to place over the joints. My reason at the time for using biscuit joints was so I could lay the molds accurately down onto the top of the plans.
I became obsessed with accuracy and bought aluminium channel to allow me screw a straight edge over the FSP so that I could align the bottom of the mold on the line which represented the jig side beam.
Accuracy - John had warned me at the workshop about the cone of accuracy - a half millimeter out at one end of the boat could wind up to by 8 millimeters at the other end... perhaps an extreme example, but I got the point and heeded the warning!
Cutting the molds in pairs on my new jig saw proved quite satisfying, but I struggled to understand which marks I needed to transfer to the molds, so I ended up copying the entire plans on to the molds.
When I was finished with the molds, I re-read the introduction on the plans which stated that the boat is built over 7 molds, 3 of which are permanent frames and 4 and just for the jig....I had built 5 out of spruce, so I had missed that in fact #6 was a permanent frame to be built out of marine ply and reinforced with DF cheeks.
It was about 3 months later when one of the molds fell down from the loft in my workshop that the folly of relying on biscuit joints alone was evidenced. So I reinforced each component with an additional brace. Also the full import of the 18% MC of the spruce revealed itself when I saw how nicely warped some of the molds had become when they dried out! That didn't prove to be a problem as I was able to straighten them out when placing them on the strongback / jig.
One mold does deserve special mention - #14. When you come to positioning the transom and the transom knee, you need to cut a section out of the top of the mold to allow the knee sit in its correct place. As I write I don't have the plans in front of me, but I am 90% certain that this is not explicit on the plans. A seasoned boat builder wouldn't think twice, but for a first timer, it took me a while and some advice from Bob to go ahead and cut out the recess.
Building Molds
John shows how to create your own Bevel Boss in his book, but this tool has proven to be a very accurate companion for me and I am doubtful if I could have recreated this with the same level of accuracy.
The biscuit joints proved to be insufficient and unnecessary so I ended up adding the blocks to place over the joints. My reason at the time for using biscuit joints was so I could lay the molds accurately down onto the top of the plans.
I became obsessed with accuracy and bought aluminium channel to allow me screw a straight edge over the FSP so that I could align the bottom of the mold on the line which represented the jig side beam.
Accuracy - John had warned me at the workshop about the cone of accuracy - a half millimeter out at one end of the boat could wind up to by 8 millimeters at the other end... perhaps an extreme example, but I got the point and heeded the warning!
Cutting the molds in pairs on my new jig saw proved quite satisfying, but I struggled to understand which marks I needed to transfer to the molds, so I ended up copying the entire plans on to the molds.
When I was finished with the molds, I re-read the introduction on the plans which stated that the boat is built over 7 molds, 3 of which are permanent frames and 4 and just for the jig....I had built 5 out of spruce, so I had missed that in fact #6 was a permanent frame to be built out of marine ply and reinforced with DF cheeks.
It was about 3 months later when one of the molds fell down from the loft in my workshop that the folly of relying on biscuit joints alone was evidenced. So I reinforced each component with an additional brace. Also the full import of the 18% MC of the spruce revealed itself when I saw how nicely warped some of the molds had become when they dried out! That didn't prove to be a problem as I was able to straighten them out when placing them on the strongback / jig.
One mold does deserve special mention - #14. When you come to positioning the transom and the transom knee, you need to cut a section out of the top of the mold to allow the knee sit in its correct place. As I write I don't have the plans in front of me, but I am 90% certain that this is not explicit on the plans. A seasoned boat builder wouldn't think twice, but for a first timer, it took me a while and some advice from Bob to go ahead and cut out the recess.
![]() |
This is the mold in action showing how the transom knee sits into the top of the mold. |
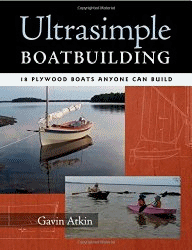
Subscribe to:
Post Comments (Atom)
No comments:
Post a Comment