Tuesday, March 19, 2013
Browse »
home»
Sheer clamps, Floors and Moving Stations!
The cold weather has slowed progress which is why it's been a while since I have updated the blog. I purchased a Far InfraRed panel which I suspended over the boat - this is an efficient way of getting the wood up to temperature for epoxy gluing.
Since the last post I have installed the sheer clamps. The instructions suggest making it out of 2 laminations, but I had a few break while bending, so I opted to use 3 laminations. That made the process slower as I had to glue up each lamination separately and wait a day in between, which was effectively 6 elapsed days. The sheer clamps however fitted snugly and look robust.
The next phase was to install the floors either side of the trunk. This proved quite tedious as hopping in and out of the boat slows down progress considerably - so I was delighted when our neighbour's son Eoin volunteered to help. We have managed to get the floors dry fitted and screwed to the hull and also the spacers and log cleat which ties the whole assembly together. Despite making the laminated floors over the hull before planking, they still needed refining and scribing to get an exact fit.
While examining the plans and ensuring that we had marked out the positions for the keel bolts, I became suspicious of some dimensions for station #6. It seems that I made a rookie mistake of assuming that all stations were 24" apart when I set up my jig and molds. In fact, all except station # 6 are 24" apart, while 6 is 20" aft of station 4, which meant that my forward bulk head would have been too far aft.

So after sleeping on the problem I decided to take out the #6 web frame. This is where once again the Bosch Multi tool saved my bacon and allowed me to cut effortlessly through the joints without damaging the hull planks whatsoever. It really is a remarkable tool...
I managed to get the old frame out of the hull intact and thought that I may be able to re-use it by marking it against the new template made, but the hull narrows by some 1 1/4" so it wasn't a runner. However I don't believe there is any need to remake a frame as the bulkhead with some cleats will be more than strong enough on its own, the frame's purpose no longer really required, as it was initially for shaping the hull while planking. (need to check with my friendly designer John Brooks)
I made a template and used small lengths of 1/4" ply hot glued to it to copy the inside shape of the hull faithfully. It was a slow process, but gave me an accurate shape in the end. I will now cut the bulkhead out from 1/2" material, so by the next post you should see it fitted.
Here you can see the hull where the old station has been removed - this is before I dressed the planks with a light sanding which removed all blemishes. Can't speak highly enough of this Bosch Multi Tool.
It looks like I will get off lightly with this mistake as I didn't take any other references from station 6, except for the hull is now about 1 1/4" narrower at this point. The lines of the hull look great so I am hoping that this slight modification will only ensure greater streamlining and a faster hull!!
This shot was taken just to re-emphasize the Houdini like cramped working conditions:-
Sheer clamps, Floors and Moving Stations!
![]() |
Far Infra Red Heating Panel |
The next phase was to install the floors either side of the trunk. This proved quite tedious as hopping in and out of the boat slows down progress considerably - so I was delighted when our neighbour's son Eoin volunteered to help. We have managed to get the floors dry fitted and screwed to the hull and also the spacers and log cleat which ties the whole assembly together. Despite making the laminated floors over the hull before planking, they still needed refining and scribing to get an exact fit.
While examining the plans and ensuring that we had marked out the positions for the keel bolts, I became suspicious of some dimensions for station #6. It seems that I made a rookie mistake of assuming that all stations were 24" apart when I set up my jig and molds. In fact, all except station # 6 are 24" apart, while 6 is 20" aft of station 4, which meant that my forward bulk head would have been too far aft.

So after sleeping on the problem I decided to take out the #6 web frame. This is where once again the Bosch Multi tool saved my bacon and allowed me to cut effortlessly through the joints without damaging the hull planks whatsoever. It really is a remarkable tool...
Hull cleaned up after frame removal |
I managed to get the old frame out of the hull intact and thought that I may be able to re-use it by marking it against the new template made, but the hull narrows by some 1 1/4" so it wasn't a runner. However I don't believe there is any need to remake a frame as the bulkhead with some cleats will be more than strong enough on its own, the frame's purpose no longer really required, as it was initially for shaping the hull while planking. (need to check with my friendly designer John Brooks)
Template used to measure Bulkhead at new position |
I made a template and used small lengths of 1/4" ply hot glued to it to copy the inside shape of the hull faithfully. It was a slow process, but gave me an accurate shape in the end. I will now cut the bulkhead out from 1/2" material, so by the next post you should see it fitted.
Here you can see the hull where the old station has been removed - this is before I dressed the planks with a light sanding which removed all blemishes. Can't speak highly enough of this Bosch Multi Tool.
It looks like I will get off lightly with this mistake as I didn't take any other references from station 6, except for the hull is now about 1 1/4" narrower at this point. The lines of the hull look great so I am hoping that this slight modification will only ensure greater streamlining and a faster hull!!
This shot was taken just to re-emphasize the Houdini like cramped working conditions:-
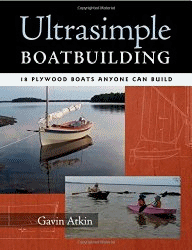
Subscribe to:
Post Comments (Atom)
No comments:
Post a Comment