Thursday, January 16, 2014
Browse »
home»
Hull fairing, DWL and machining lead....
Spent a few days fairing the hull and sanding, I am using a a Hempel epoxy fairing compound, which takes a bit of practice to get get right. Initially I think I was spreading it too thick, until I realized that it can be skimmed on very finely almost like a thin layer of paint with a stiff plastic spreader - leading to less sanding
and a smoother finish. Having sheathed the rudder and centreboard I was left with lots of minor blemishes which the fairing compound rectified. I practiced on the centreboard as this will never be seen again!
Also I sealed the edges of the ply stakes with neat epoxy. Once again, my wife Siobhan was right! "Why don't you just use a big syringe to apply the neat epoxy to the edges?" Well thinking I knew better, I brushed it on liberally and spent the next two days scraping and sanding off the excess....
Here's a picture of the hull with the laps sealed prior to sanding.
Next came to finding the DWL on the hull. Of course all the meticulously DWL lines I had on virtually every part of the hull had long been consigned to the sanding dust heap...so with Brian's assistance we reworked the DWL by taking various measurements from the plans and then using Brian's fancy self leveling laser, we scribed the DWL on the hull.
This photo doesn't really depict the DWL very well, as my long serving Nikon D70 finally died, so I have been taking pics with my Samsung smart phone which struggles a bit in the dark.
However, we were able to get a laser line running from stem to transom and they matched up quite well with the marks we made from the plans.
Here's Brian with his self levelling laser
Next step was to clean up the lead keel. I needed to countersink the holes to accept the bronze washers. The 1/2" washers have a 32mm external diameter and my Forster bit collection had a 30mm and 35mm, but no 32mm. So I cut the holes out to 30mm and used a router with a straight cutting bit to widen and clean out the holes, which worked surprisingly well.
I had some holes, hollows and dips in the keel which I filled with molten lead and faired with epoxy. I have more work to do before it is ready to fix permanently onto the hull.
I have been getting some good advice from fellow glued lapstrake builders on the yahoo forum. I have now decided to sheath the garboards with epoxy and glassfibre, I only wish I came to that conclusion sooner, having spent so much time fairing the garboards already...
Also looking for some detailed advise on how to use slings to turn the hull with the lead keel bolted, so feel free to comment if you can offer suggestions.
Today was a busy day for the couriers....my order from Rutlands Tools arrived. Pride of place was a set of Japanese pull saws and a Quansheng #4 smoothing plane, plus a box of 170 assorted bradpoint drills and various bits and pieces for jig making. Then some parts arrived from Classic Marine UK - keel banding, bronze tow eye, bronze dome nuts for the inside of the chain plates and some latches for the lockers - which is quite exciting. I'll take some photos tomorrow and post them (done!). I am in the process of ordering the rigging parts from Classic Marine who are really great people to deal with - very helpful even to first timers like myself. I'll write this up when the parts arrive, but so far it looks like they will supply an authentic rig.
Hull fairing, DWL and machining lead....
and a smoother finish. Having sheathed the rudder and centreboard I was left with lots of minor blemishes which the fairing compound rectified. I practiced on the centreboard as this will never be seen again!

Here's a picture of the hull with the laps sealed prior to sanding.
Next came to finding the DWL on the hull. Of course all the meticulously DWL lines I had on virtually every part of the hull had long been consigned to the sanding dust heap...so with Brian's assistance we reworked the DWL by taking various measurements from the plans and then using Brian's fancy self leveling laser, we scribed the DWL on the hull.
This photo doesn't really depict the DWL very well, as my long serving Nikon D70 finally died, so I have been taking pics with my Samsung smart phone which struggles a bit in the dark.
However, we were able to get a laser line running from stem to transom and they matched up quite well with the marks we made from the plans.
Here's Brian with his self levelling laser
Next step was to clean up the lead keel. I needed to countersink the holes to accept the bronze washers. The 1/2" washers have a 32mm external diameter and my Forster bit collection had a 30mm and 35mm, but no 32mm. So I cut the holes out to 30mm and used a router with a straight cutting bit to widen and clean out the holes, which worked surprisingly well.
I had some holes, hollows and dips in the keel which I filled with molten lead and faired with epoxy. I have more work to do before it is ready to fix permanently onto the hull.
I have been getting some good advice from fellow glued lapstrake builders on the yahoo forum. I have now decided to sheath the garboards with epoxy and glassfibre, I only wish I came to that conclusion sooner, having spent so much time fairing the garboards already...
Also looking for some detailed advise on how to use slings to turn the hull with the lead keel bolted, so feel free to comment if you can offer suggestions.

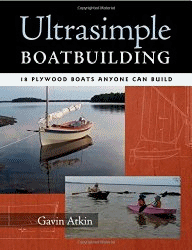
Subscribe to:
Post Comments (Atom)
No comments:
Post a Comment